
Múnich. En el Campus de Manufactura Aditiva en Oberschleissheim, BMW Group utiliza el innovador sistema “live wire” para producción aditiva de componentes y herramientas metálicas para vehículos. En la manufactura aditiva por arco de alambre (WAAM), se derrite un alambre de aluminio o de un material similar utilizando un arco eléctrico. Luego, un robot controlado por software coloca una gran cantidad de soldaduras una encima de la otra con precisión, hasta que se completa el componente completo. Debido a que la pieza se forma capa por capa, no es necesario prestar atención a la desmoldabilidad, son posibles estructuras huecas con una relación óptima entre rigidez y peso.
Esto significa que los componentes pueden ser más ligeros y rígidos que las piezas de fundición a presión comparables actualmente fabricadas en producción en serie. También se pueden producir de manera más sostenible gracias a un menor consumo de energía y menos desperdicio de material. En el futuro, se planea utilizar componentes fabricados utilizando el proceso WAAM en vehículos de producción de BMW Group.
El proceso WAAM es particularmente adecuado para componentes grandes
La gran anchura y altura de una sola soldadura significa que los componentes se pueden producir extremadamente rápido utilizando WAAM. A diferencia de la fusión por haz láser, que ya se utiliza en la producción de prototipos y pequeñas series en el BMW Group, WAAM es particularmente adecuado para componentes más grandes. Los espesores de pared típicos son adecuados para componentes en las áreas de la carrocería, el tren motriz y el chasis. Sin embargo, también se pueden fabricar herramientas y dispositivos utilizando este proceso de alta tecnología, que también se utiliza en la industria aeronáutica.
Desarrollo en el Campus de Manufactura Aditiva
BMW Group está probando este proceso en el Campus de Manufactura Aditiva en Oberschleissheim, donde ha reunido las actividades de producción, investigación y formación en esta área bajo un mismo techo. Con más de 30 años de experiencia, la empresa es pionera en el área de la manufactura aditiva, comúnmente conocida como impresión 3D. Los empleados de BMW Group se han centrado en el proceso WAAM, también conocido como soldadura de construcción, desde 2015. Una celda WAAM para la producción de componentes de prueba ha estado en uso allí desde 2021. Una de estas aplicaciones de ejemplo es un soporte de amortiguador, que, en extensas pruebas en el banco de pruebas, se está comparando con el componente de producción en serie fabricado a partir de fundición a presión de aluminio. “En esta etapa temprana ya está claro que el proceso WAAM puede reducir las emisiones en el proceso de producción. El menor peso de los componentes, su ventajosa relación de uso de materiales y la opción de utilizar energía renovable significa que los componentes pueden ser producidos de manera más eficiente”, dijo Jens Ertel, Jefe de Manufactura Aditiva de BMW. La siguiente etapa de desarrollo en el camino hacia la producción en serie es probar los componentes en el vehículo, lo cual comenzará en un futuro cercano.
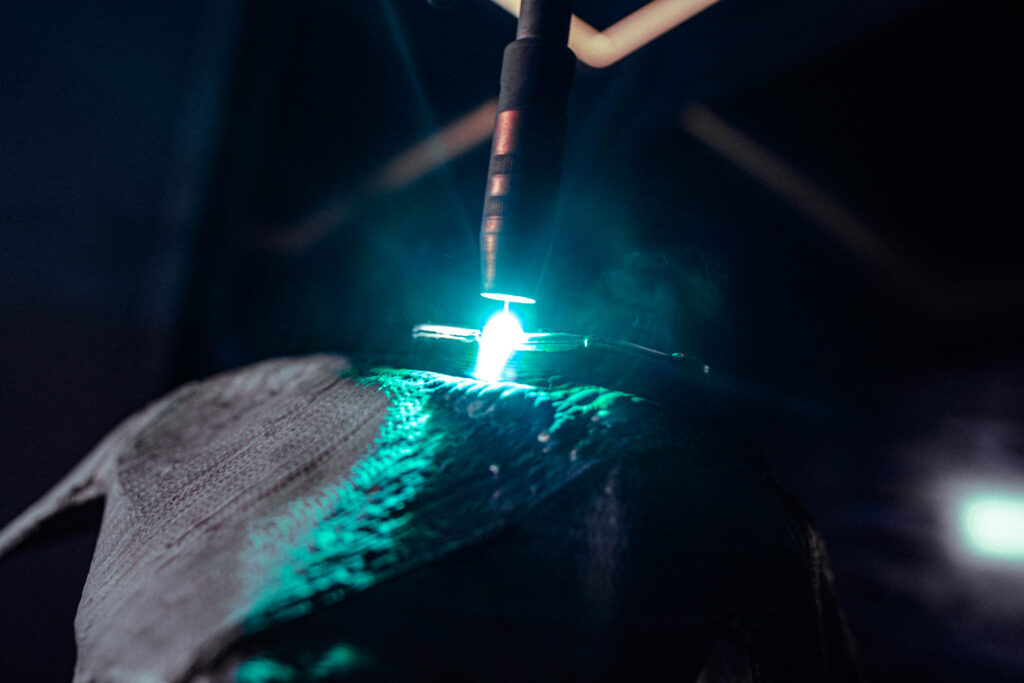
Las soldaduras más anchas en el proceso WAAM significan que las superficies de los componentes no son lisas, sino ligeramente onduladas y deben ser terminadas en áreas críticas. Sin embargo, los ingenieros del BMW Group pudieron demostrar que los componentes de WAAM pueden ser utilizados para cargas altas, incluyendo cargas cíclicas, incluso sin tratamiento posterior de la superficie. Los parámetros del proceso optimizados son cruciales para garantizar la durabilidad directamente desde la producción, por lo que la combinación del proceso de soldadura y la planificación de la trayectoria del robot deben ser coordinados de manera óptima.
Configuración con diseño generativo y algoritmos
Para aprovechar al máximo los componentes producidos en el proceso WAAM, es fundamental combinar el proceso de manufactura con un nuevo diseño general de componentes. Con este fin, BMW Group continúa acelerando el uso del diseño generativo. Aquí, la computadora utiliza algoritmos para diseñar componentes optimizados en función de los requisitos específicos. Estos algoritmos se desarrollan en estrecha colaboración con equipos interdisciplinarios y están inspirados en parte por procesos evolutivos en la naturaleza. Al igual que en las estructuras biónicas, el primer paso es utilizar solo el material que se requiere realmente para la topología del componente, y durante el ajuste fino en el segundo paso, el componente se refuerza solo donde es necesario. Esto resulta en componentes más ligeros y rígidos, así como una mayor eficiencia y una mejora en la dinámica del vehículo.
“Es impresionante ver cómo la tecnología WAAM ha evolucionado desde la investigación hasta convertirse en una herramienta flexible no solo para componentes de prueba, sino también para componentes de producción en serie. El uso de métodos de diseño generativo nos permite aprovechar al máximo la libertad de diseño y, por lo tanto, el potencial de la tecnología. Eso era impensable hace apenas unos años”, dijo Karol Virsik, Jefe de Investigación de Vehículos del Grupo BMW.
Los procesos de producción pueden complementarse entre sí
Diferentes procesos de producción aditiva no necesariamente compiten entre sí, más bien deben considerarse como complementarios. Por ejemplo, la fusión por haz láser seguirá siendo más ventajosa que el proceso WAAM en cuanto al nivel más alto de resolución de detalles. Sin embargo, en cuanto al tamaño posible del componente y la velocidad de deposición, la manufactura aditiva con arco de alambre es superior. El Grupo BMW planea inicialmente la producción centralizada de componentes WAAM en Oberschleissheim, en el futuro también es posible la producción en otras ubicaciones y el uso de la tecnología por parte de proveedores. Además, incluso sería concebible producir componentes individuales directamente en la línea de ensamblaje utilizando este proceso y fabricar diferentes piezas sin necesidad de nuevas herramientas, simplemente cambiando el software. La sostenibilidad también puede mejorarse aún más aumentando el uso de metales reciclados.
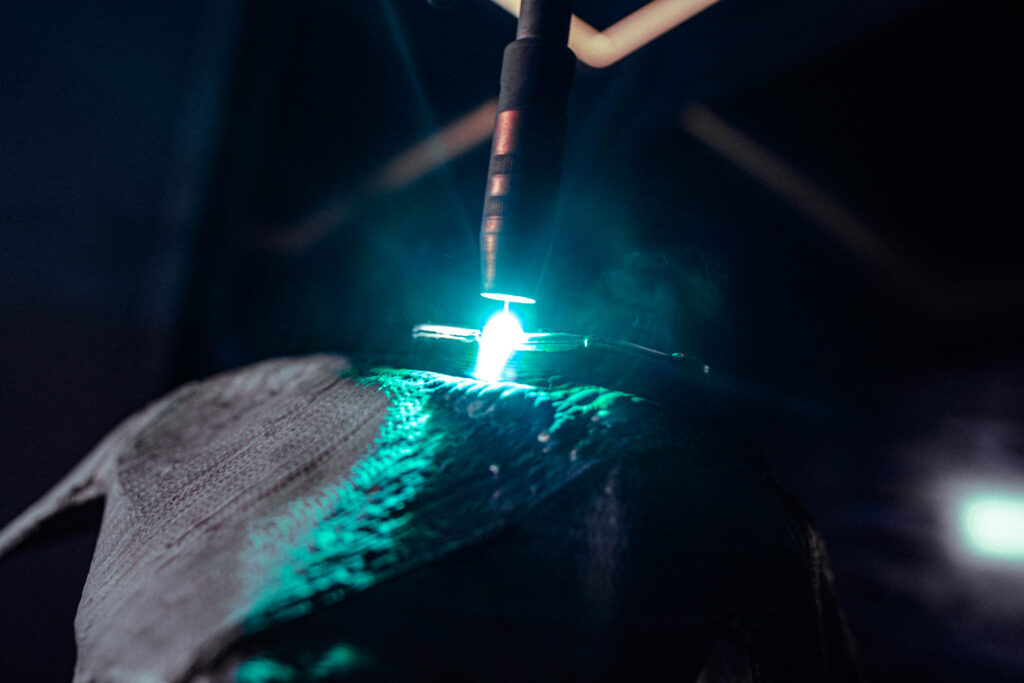
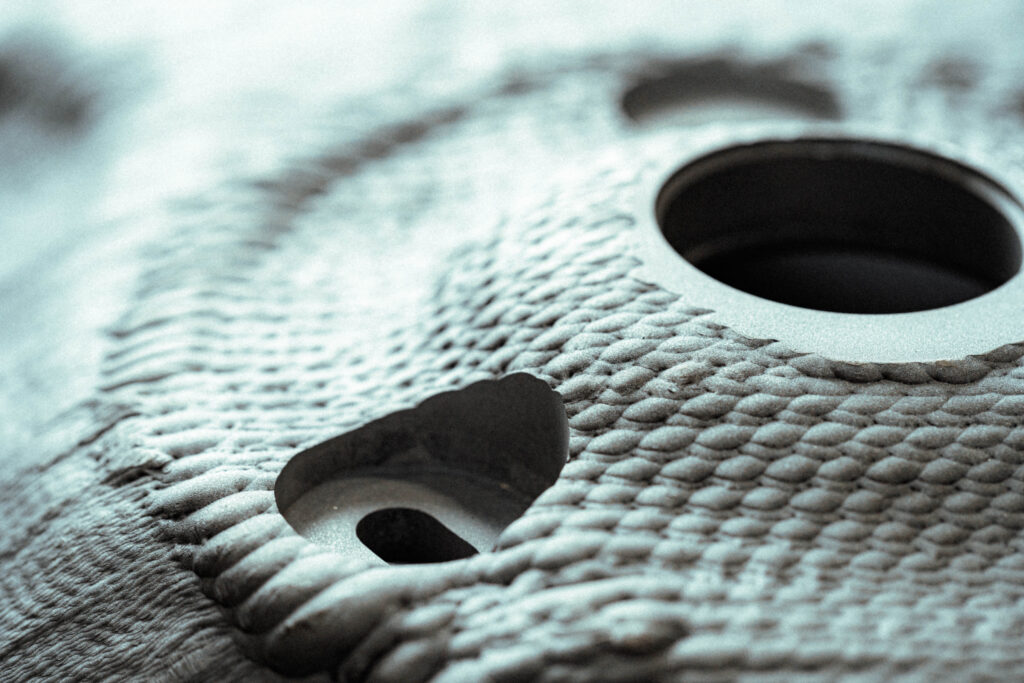
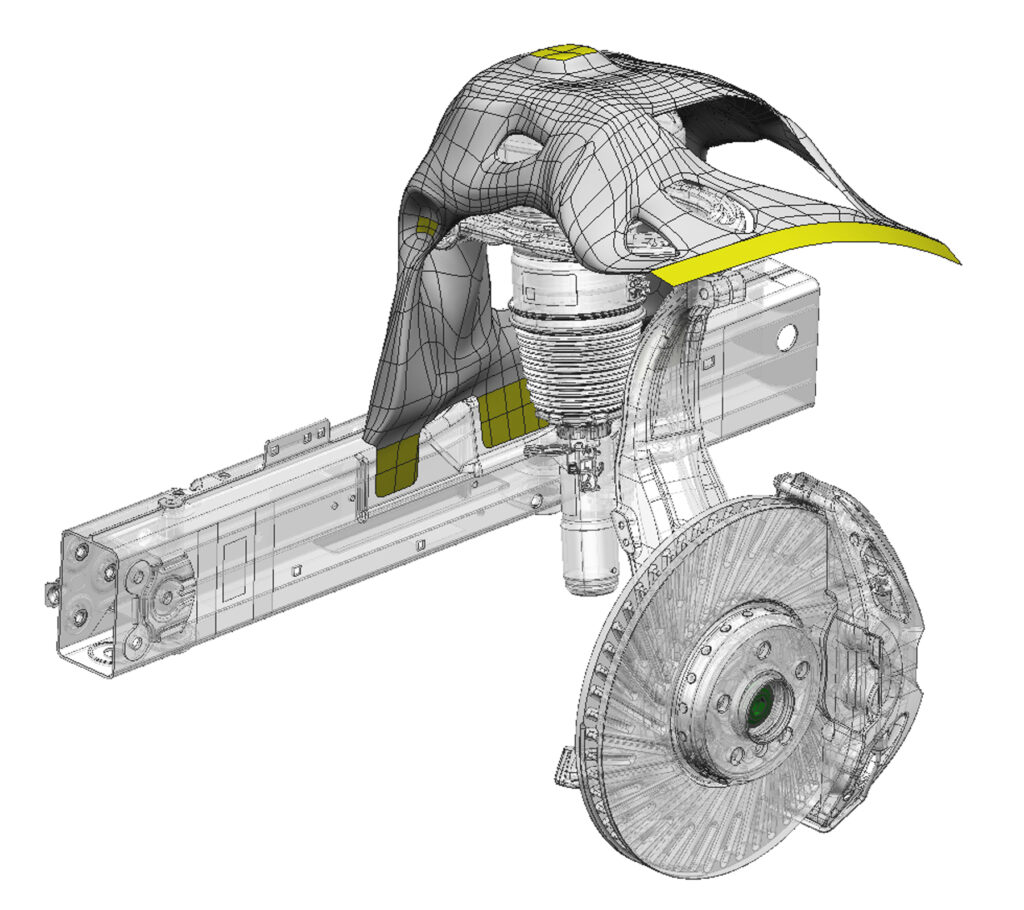
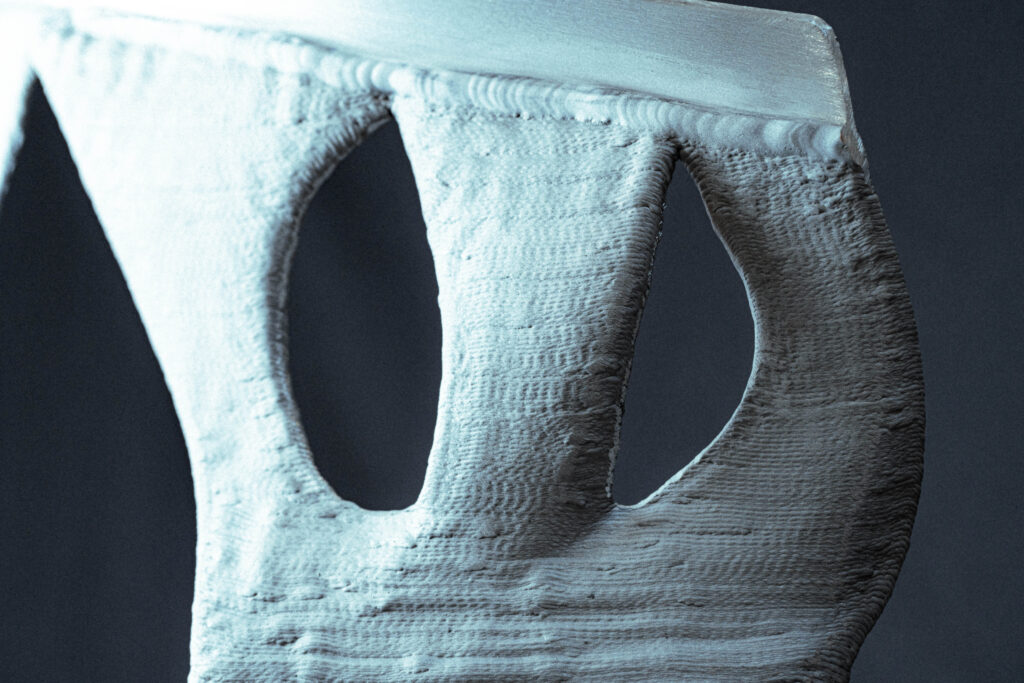
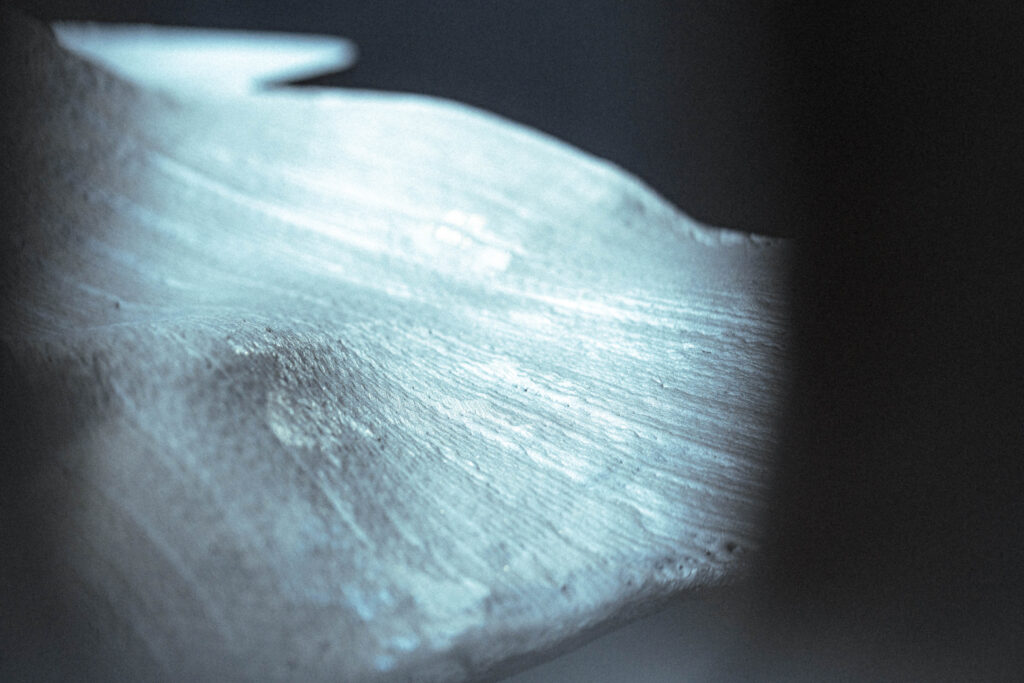
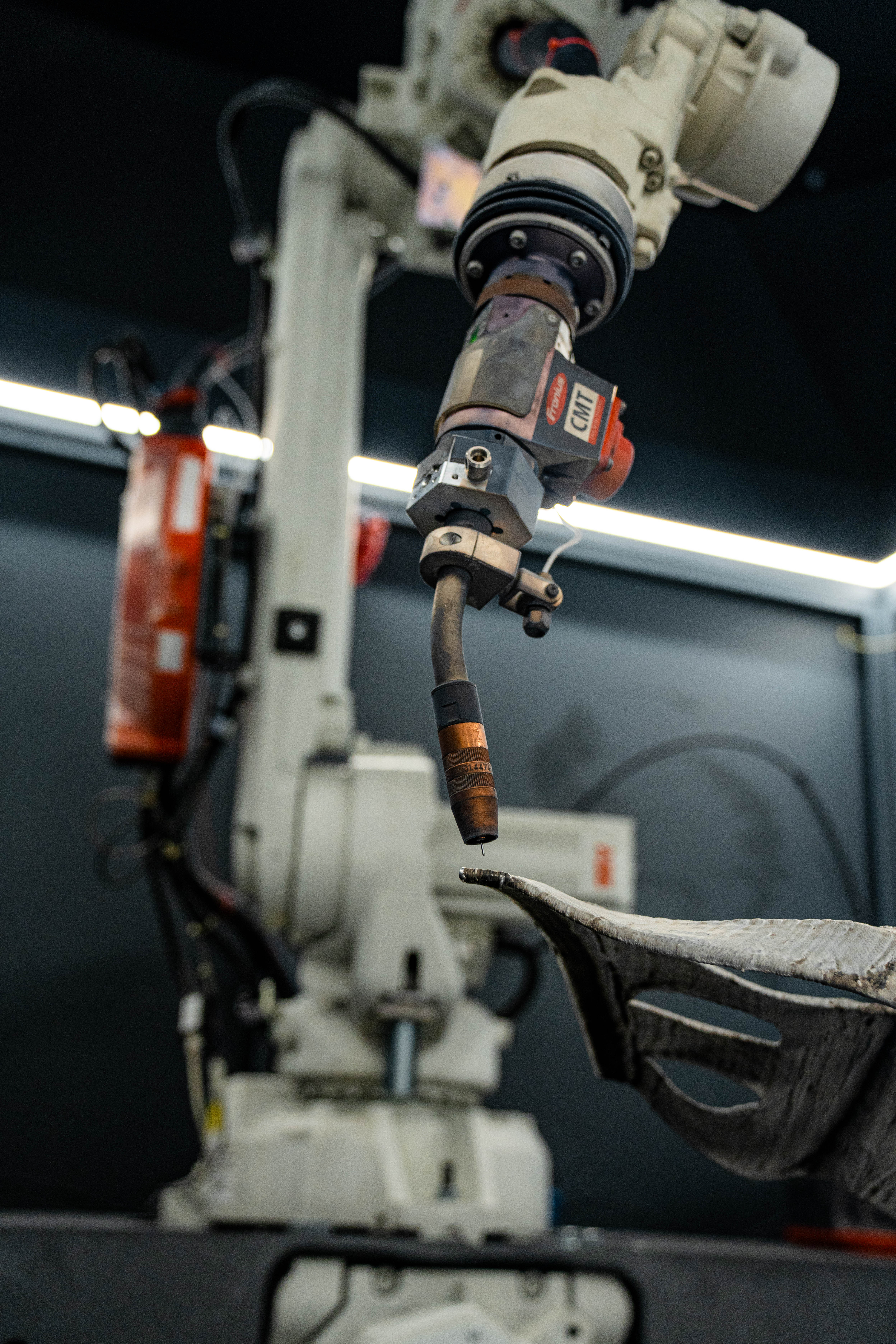
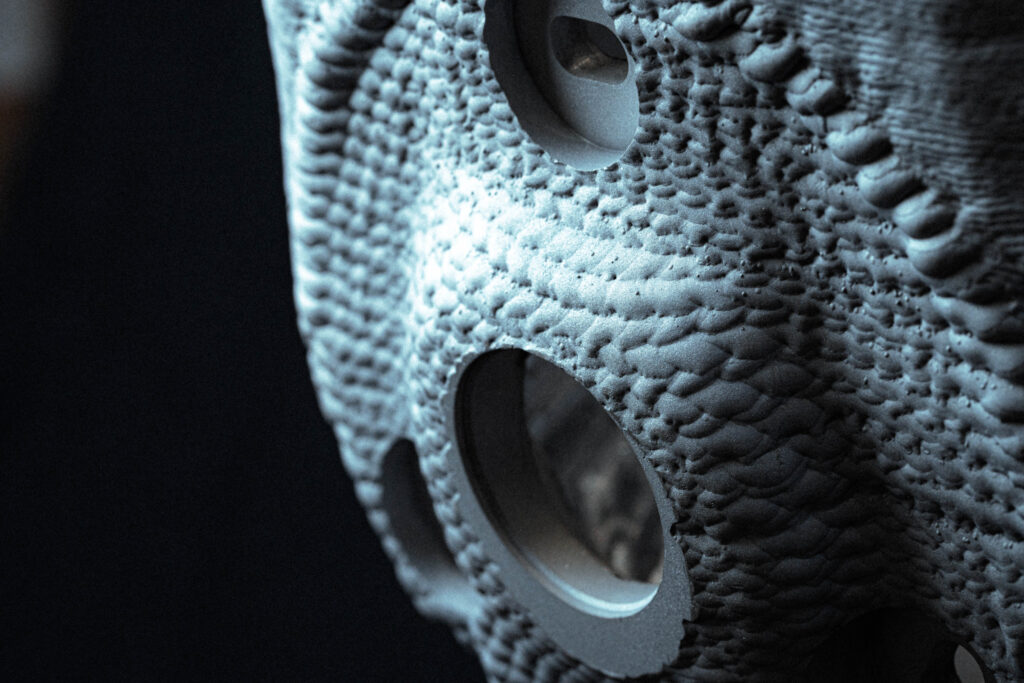
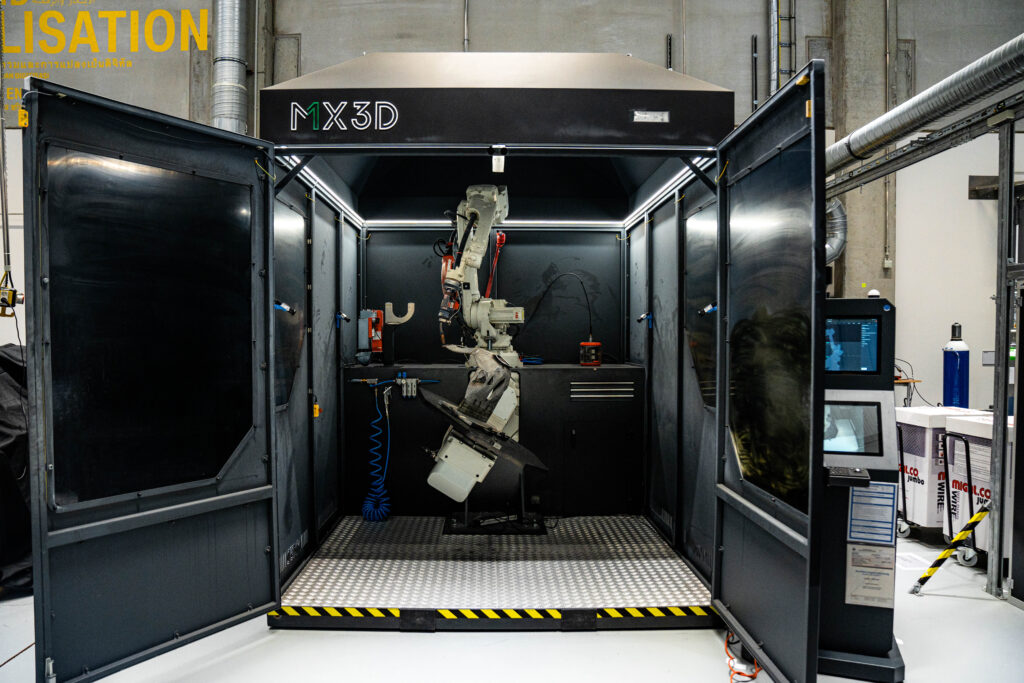
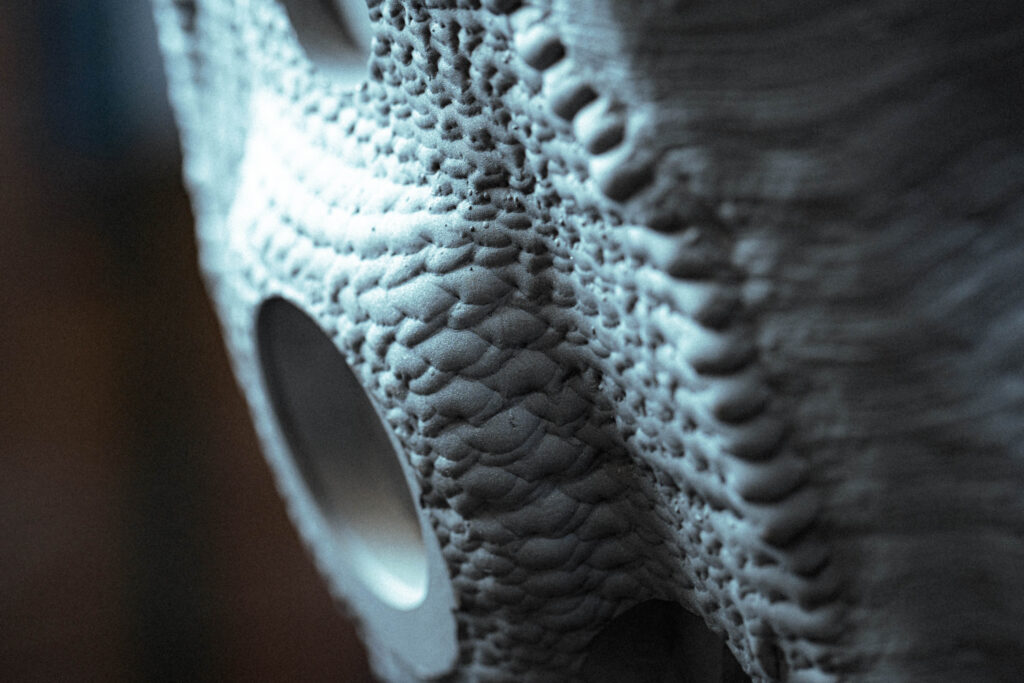
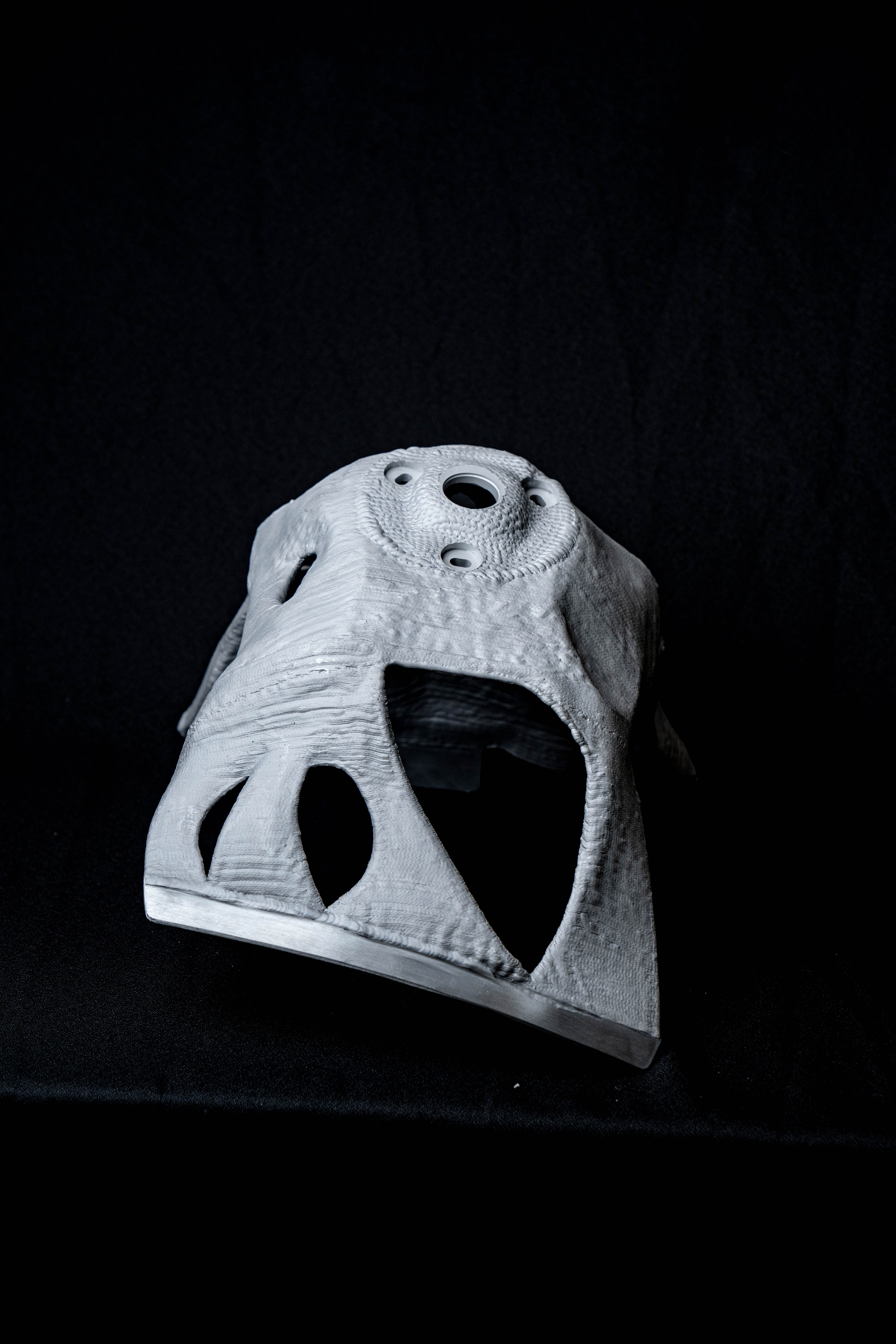
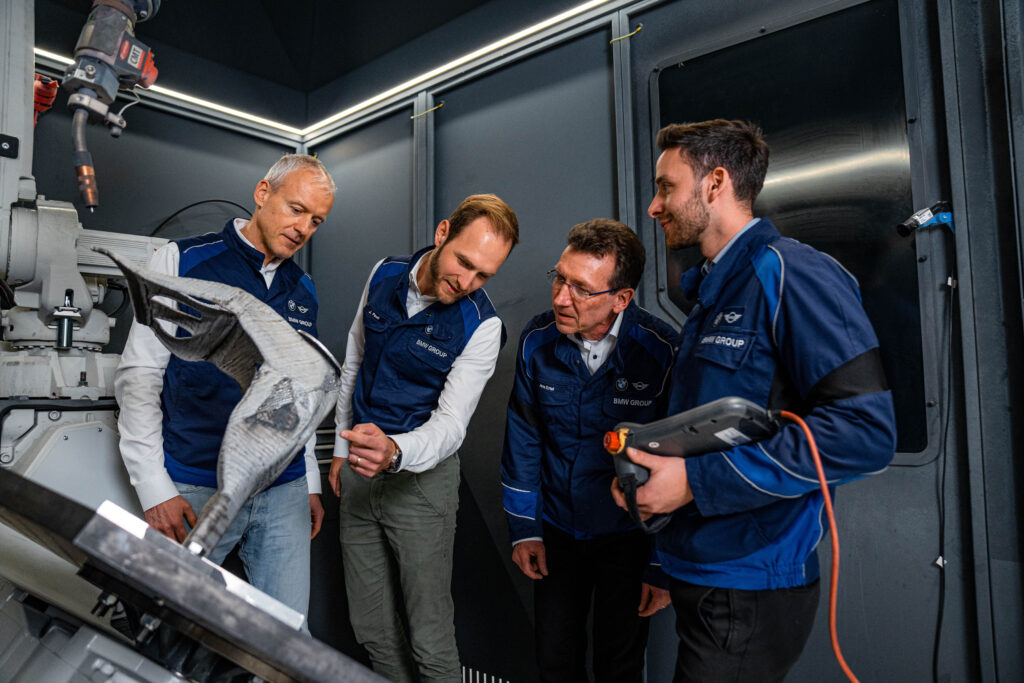
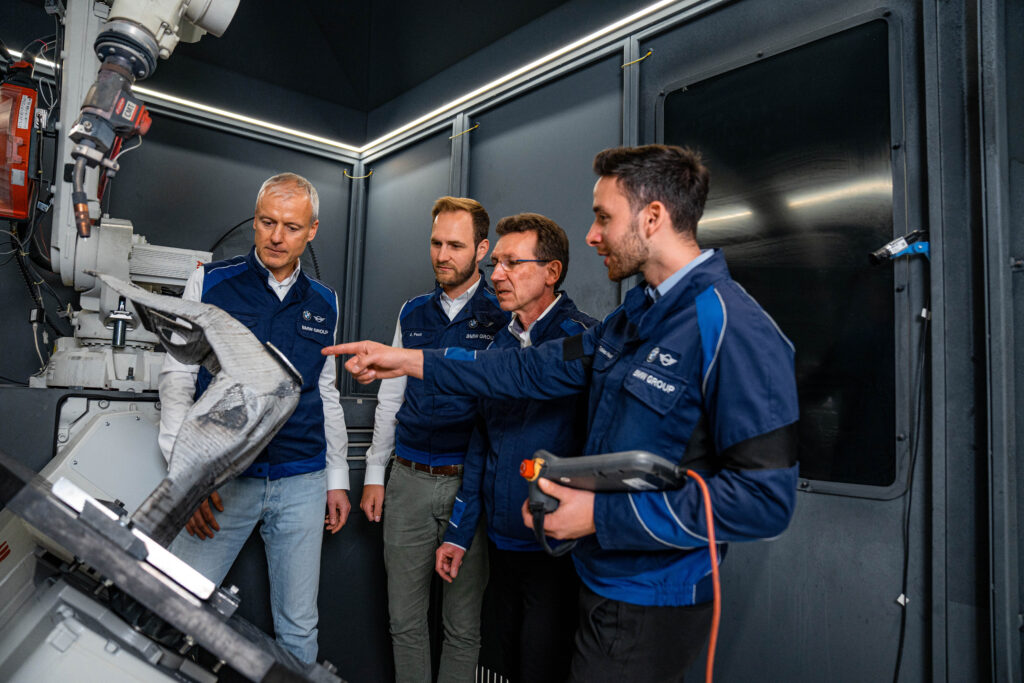